OEE Nedir? (Overall Equipment Effectiveness)
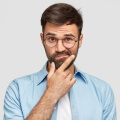
Yazar
Albert FloresOEE (Toplam Ekipman Etkinliği), Nakajima (1988) tarafından TPM konsepti içinde bir KPI (performans göstergesi) olarak tanıtılmıştır. Makinelerin kullanılabilirlik, performans ve kalite kayıplarını tek bir parametre ile ölçmek ve izlemek için geliştirilmiş matematiksel bir metottur. OEE, bir işletmede gerçekleştirilen üretim ile planlanan üretim arasındaki oran olarak da tanımlanır. Yönetimin gizli kapasiteyi geri kazanmasına, üretim kayıplarını azaltmasına ve ek sermaye yatırımı ihtiyacının belirlenmesine yardımcı olmaktadır. OEE yi etkileyen kayıplar aşağıdaki gibidir.
Kullanılabilirliğe etki eden kayıplar:
- Arıza Kaybı: Makine, hat ya da ekipmandaki herhangi bir beklenmeyen duruştur.
- Setup ve Ayar Kaybı: Her türlü ürün ya da versiyon geçişi sırasında yapılan fiziksel ya da formal işler için harcanan zaman kaybıdır.
- İkmal ve Doldurma Kaybı: Üretimin devam edebilmesi için gerekli malzemenin, getirilme süresi.
- Başlangıç Kaybı: Üretim öncesi makinenin hazır hale getirilmesi ya da yapılan hazırlıkları kapsar.
Performansa etki eden kayıplar:
- Küçük Duruş Kayıpları: 5 dakikanın altında olan çoğu zaman operatörün müdahalesi ile çözülen küçük duruşlar ve takılmalardır.İşletmeler bu duruşları kayıt altına alamadığı için performans kaybı olarak görünür.
- Hız Kaybı: Makinenin bilinçli olarak yavaşlatılması ya da herhangi bir problemden dolayı tam hızda çalışamama durumudur
Kaliteye etki eden kayıplar:
- Hurda – Tekrar İşlem Kaybı: Müşteriye gönderilemeyecek sınıfta olan her türlü ürün ya da aynı ürüne tekrar işlem yapılması durumlarında harcanan zamandır.
OEE Nasıl Hesaplanır:
OEE hesabı, üretim tesisinin açık olduğu süreyi tanımlamak ile başlar. Bu süreye “Toplam Çalışma Süresi” denir. Toplam çalışma süresinden, daha önceden üretim yapılmaması planlanmış planlı duruşlar çıkartılarak “Planlanmış Çalışma Süresi” hesaplanır. Planlanmış çalışma süresinden, üretim sırasında yaşanan ve duruş olarak daha önceden planlanmamış plansız duruşlar çıkartılarak “Çalışma Süresi” hesaplanır. Fiilen üretimin yapıldığı kabul edilen çalışma süresinden, üretim hızını negatif yönde etkileyen ve teorik üretim hızından uzaklaşmaya neden olan hız kayıpları ve küçük duruşları çıkarttığımız durumda “Net Çalışma Süresi” hesaplanır. Net çalışma süresi içinde yapılan üretimden, aynı zaman diliminde üretilmiş ilk seferde doğru üretilemeyen ürünler için harcanmış zaman dilimini çıkarttığımız durumda “Değer Katan Süre” hesaplanır.
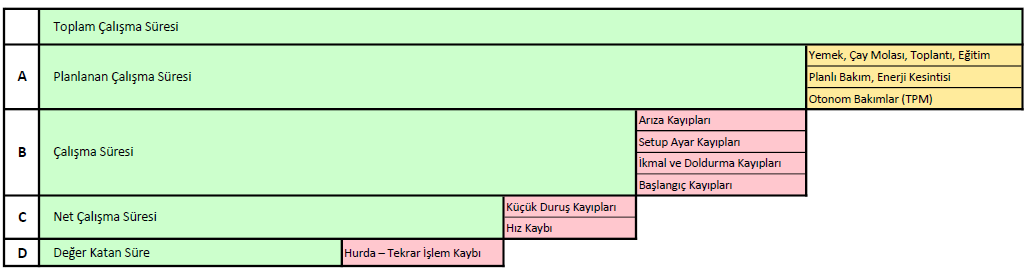
Kullanılabilirlik = Çalışma Süresi / Planlanan Üretim Süresi * 100
Performans = Net Çalışma Süresi / Çalışma Süresi * 100
Kalite = Değer Katan Süre / Net Çalışma Süresi * 100
OEE = Kullanılabilirlik * Performans * Kalite / 10.000
OEE değeri yukarıdaki üç faktörün çarpımı sonucunda elde edilir. Bu değerlerin anlamlılığı literatürde ideal değer olarak da kabul edilen %85 ile kıyaslanarak yorumlanabilmektedir. %85 ten küçük olan değerlerde, üretim hatlarının etkin bir şekilde kullanılmadığını göstermektedir. Ekipman etkinliğini (OEE) artırmak için işletmelerin bakım çalışmalarına daha fazla önem vermeleri gerekmektedir. Bir makine ve ekipmanın; atıl kalması, belirlenen adette üretim yapamaması, kaliteli bir ürün elde edememesi etkin bir bakım faaliyeti yapılmadığının göstergesidir. OEE çalışmaları yapılmadan yönetilmeye çalışılan makine ve ekipmanların bakım maliyetleri doğrudan ve dolaylı şekilde artarak işletmeye maliyet yükü getirecektir. Maliyetlerin artması sektör içerisinde rekabet edebilme imkanını ortadan kaldıracaktır.